Das Füllrohrsystem
Die Verladung der brennbaren Flüssigkeiten in Kesselwagen wird durch das Füllrohrsystem nach dem On-Spot-Prinzip durchgeführt. Die Produkte können über verschiedene Produktleitungen und den zugehörigen Produktsammlern dem Füllrohrsystem zugeführt werden. Auf jedem Gleis kann durch ein Füllrohrsystem verladen werden. Weitere Füllrohrsysteme können auf jedem Gleis nachgerüstet werden.
Das Füllsystem wird nach jeder Beladung vollständig entleert.
Das Füllrohrsystem besteht aus:
- Füllrohrwagen
- Füllrohr
- Gelenkscheren
- Hydraulikanlage
- Pneumatikanlage
- Optional: Erdungsüberwachung
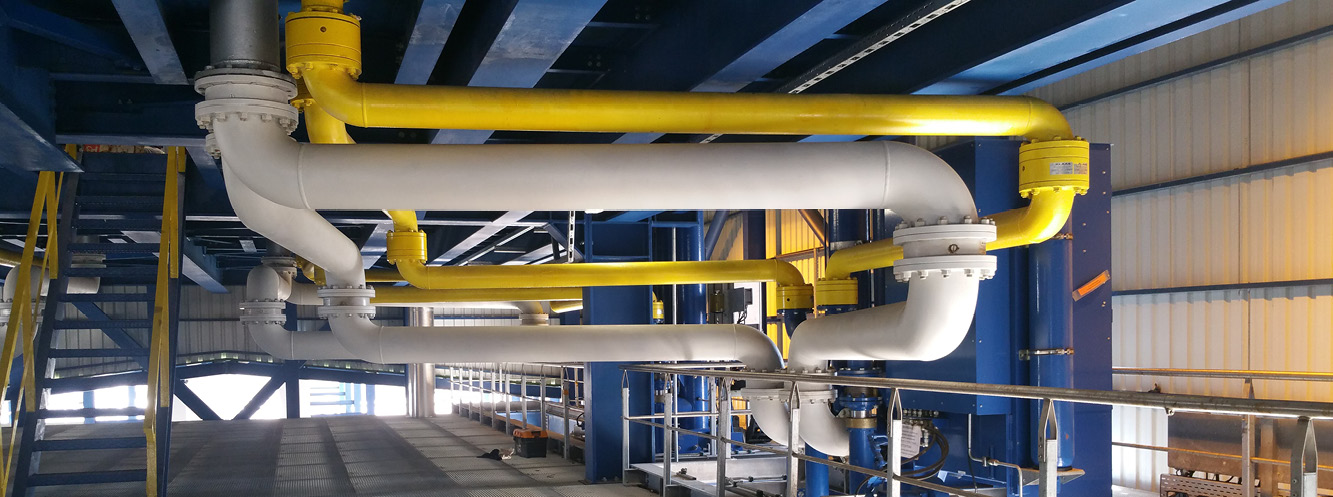
Die Füllrohre eines Gleises werden in dem Füllrohrwagen in Gleisachse nebeneinander montiert. Der Füllrohrwagen ist auf Rollen gelagert und ermöglicht über das Hydrauliksystem die Querfahrt (+/- 100 mm) und die Längsfahrt (ca. bis 10 m) der Füllrohre. Die Querfahrt wird durch ein oder zwei hydraulische Zylinder, die parallel betrieben werden, angetrieben. Die Längsfahrt wird durch einen Hydromotor angetrieben.
Die Fahrbefehle für die Quer- und Längsfahrt können durch die Bedienung des Joysticks im Steuerpult des Bedienraumes gegeben werden. Durch die Fenster des Bedienraums kann das Bedienpersonal den Füllpunkt einsehen und kann mit der Quer- und Längsfahrt das zur Verladung ausgewählte Füllrohr exakt über der Domöffnung positionieren. Die Endlagen der Längs- und Querfahrt und Mittenposition der Querfahrt werden durch Sensoren abgefragt.
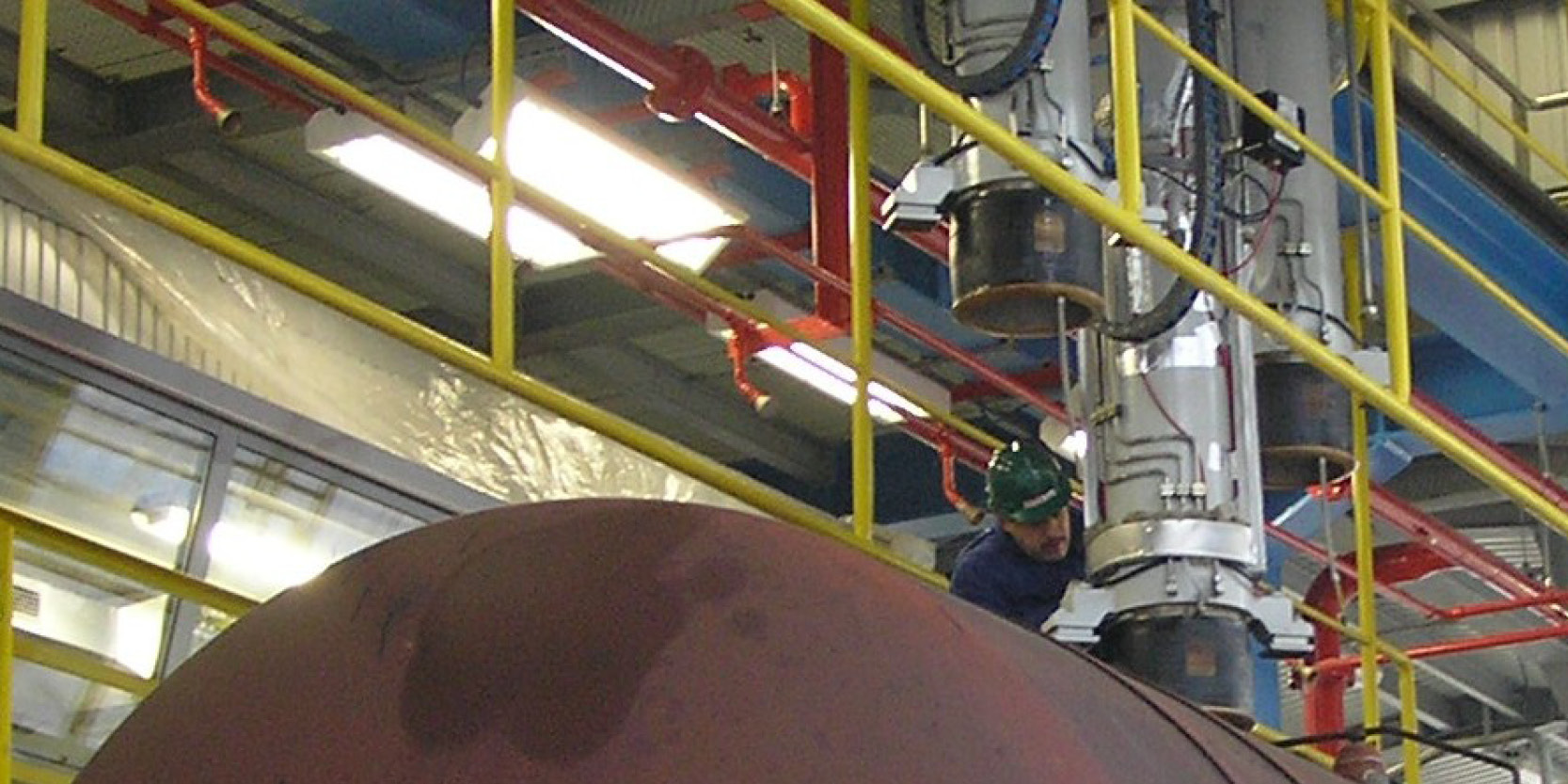
Die Füllrohre werden in einer qualitativ hochwertigen Ausführung maschinentechnisch hergestellt. Das Gewicht eines Füllrohres beträgt je nach Ausführung zwischen 1.600–2.000 kg. Die Führungsflächen sind hartverchromt und bronzegeführt. Die Wandstärken sind mit 10–20 mm je nach Füllrohrkomponente für eine sehr lange Lebensdauer ausgelegt. Bei regelmäßiger Wartung sind Standzeiten bis zu 35 Jahre möglich.
Zum Ein- und Ausfahren in den Kesselwagen sind die Füllrohre mit einem innen liegenden Hydraulikzylinder ausgestattet mit dem das Füllrohr eine Ausfahrlänge von 4.250 mm (Westeuropa), 4.700 mm (Osteuropa) bzw. entsprechend den länderspezifischen Kesselwagentypen erreicht. Die Endlagen „Füllrohr oben“ und „Füllrohr in Kesselwagen eingefahren“ werden mit Initiatoren überwacht.
In der oberen Endlage verfügt das Füllrohr über eine mechanische Arretierung.
Die Produktzuführung erfolgt durch den 200 bis 300 mm großen Füllrohrinnendurchmesser (Standardfüllrohr 230 mm) und den Produktanschlussstutzen der Gelenkscheren bzw. Teleskoprohre. Die Gasrückführung erfolgt durch das Füllrohr und das vertikale Gasteleskoprohr über den Produktanschlussstutzen der Gasgelenkschere bzw. des Gasteleskoprohres. Der am Füllrohr angebrachte aufblasbare Dichtungsbalg oder die Dichtungsplatte (osteuropäische Kesselwagen) ermöglicht die hermetische Abdichtung des Kesselwagens während der Beladung. Die Füllrohre sind mit einer Überfüllsicherung nach dem Einperlprinzip oder mit einer speziellen mechanischen Überfüllsicherungssonde und einer Drucküberwachung ausgestattet.
Alle den Kesselwagen berührenden Teile sind in Bronze ausgeführt. Die Erdung der Kesselwagen wird über Erdungskontakte an dem Füllrohr mit Aufsetzen des Füllrohres erreicht und durch ein Erdungstestgerät überwacht (automatische Erdung). Falls die Erdung des Kesselwagens durch die automatische Erdung nicht zustande kommt kann die Erdung mit dem zweiten Erdungstestgerät hergestellt werden. Die Erdungsüberwachung bei Kesselwagen ist länderspezifisch erforderlich. In Deutschland ist z. B. eine separate Erdungsüberwachung bei Kesselwagen nicht notwendig.
Weitere Überwachungen werden in dem zugehörigen Pneumatikschrank und Hydraulikschrank ausgeführt.
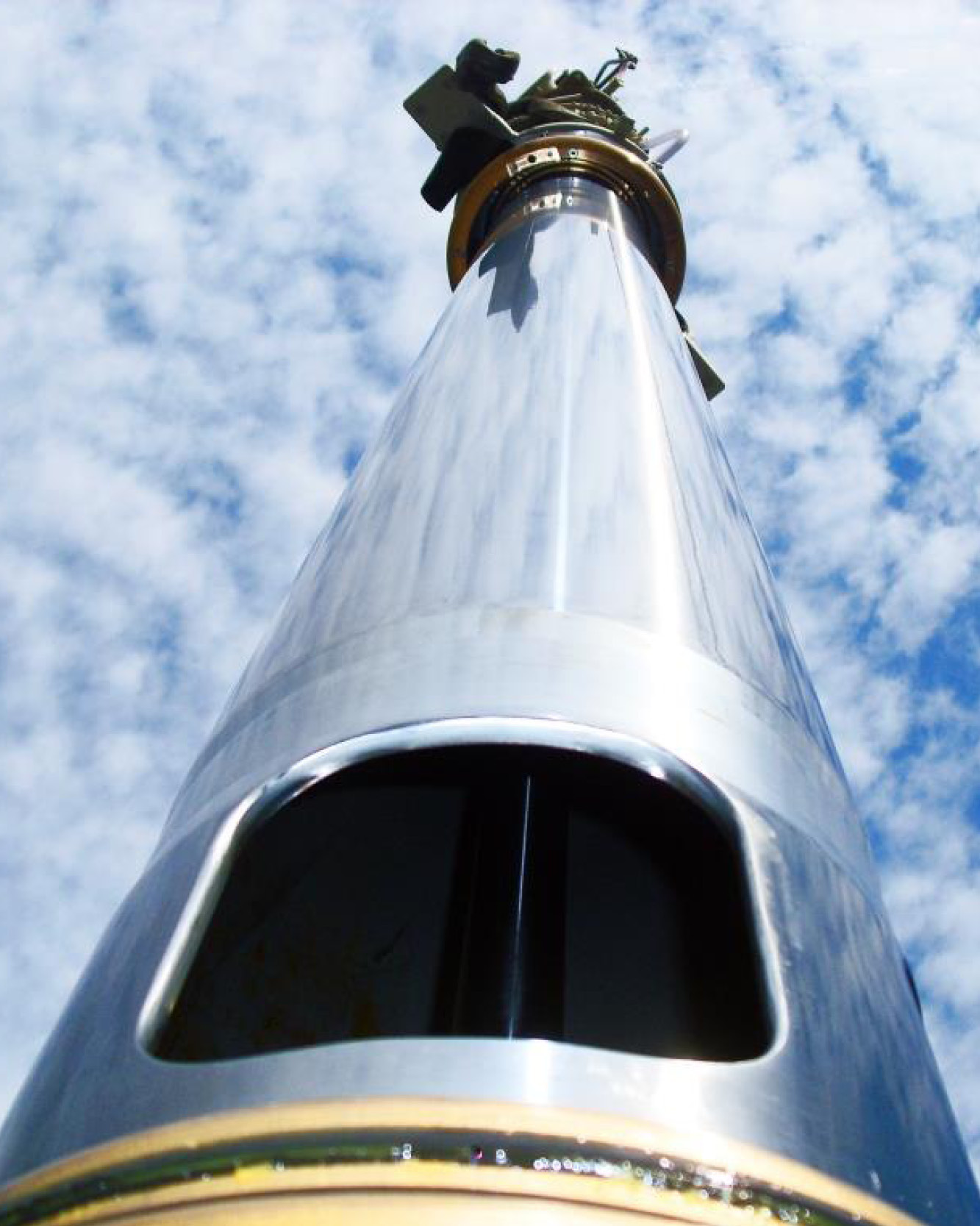
Die Entscheidung, welches System für die Verbindung der Füllrohrtechnik mit der Anlagenseite eingesetzt wird, ist abhängig vom erforderlichen Verfahrbereich der Füllrohre. Dieser Verfahrbereich ist abhängig von den Abmessungen unterschiedlicher zu beladender Kesselwagen.
Die Gasrückführung des Füllrohres ist über eine Gasgelenkschere bzw. Gasteleskoprohre an der Gasrückführungsleitung angebunden. Die Gasrückführung wird normalerweise mit pneumatisch gesteuerten Armaturen ausgestattet mit denen die Gasleitung abgesperrt werden kann. Die kontinuierliche Drucküberwachung der Gasphase im Kesselwagen und der Gasleitung schützt das Dämpfesystem vor unzulässigem Über- oder Unterdruck.
Die Füllrohre sind über Gelenkscheren bzw. Teleskoprohre an die verschiedenen Produktverteiler angebunden. Die Gelenkscheren/Teleskoprohre für Produktleitungen und Gasleitung ermöglichen die Bewegungen des Füllrohres in der horizontalen Ebene (links, rechts, vorwärts und rückwärts).
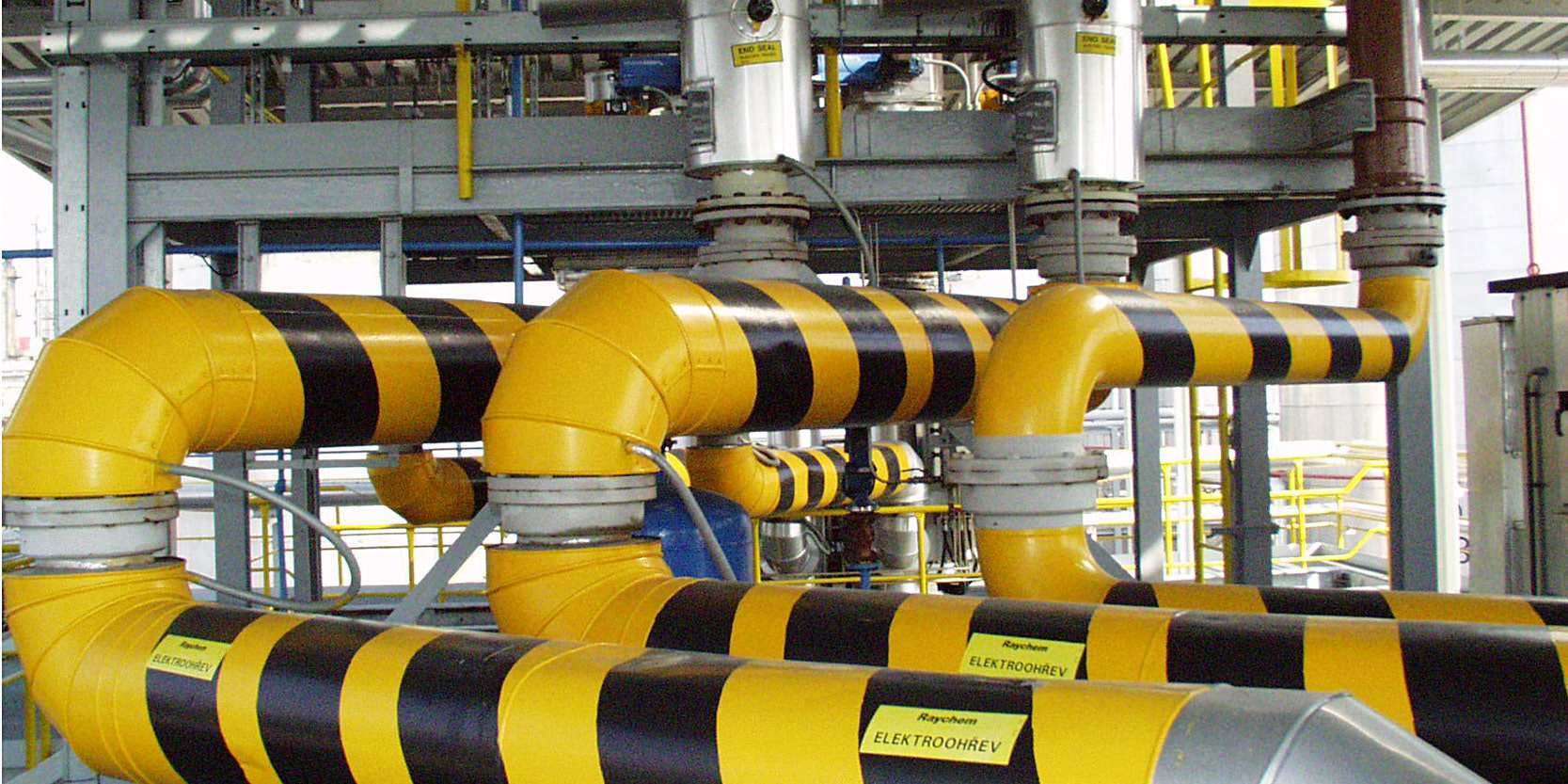
Pro Füllrohrsystem wird in der Regel eine Hydraulikanlage installiert. Die Hydraulikanlage (ausgelegt nach ATEX Richtlinien bzw. länderspezifischen Ex-Anforderungen) übernimmt die Steuerung der Füllrohrmechanik. Der für die erforderliche hydraulische Bewegung notwendige Hydraulikdruck wird durch eine Hydraulikpumpenmotor-Kombination geliefert.
Der Hydraulikmotor wird nur angesteuert, wenn durch entsprechende Funktionen Hydraulikdruck angefordert wird. Die folgenden Funktionen sind vorgesehen:
- Selektion Füllrohr
- Füllrohr aufwärts bzw. abwärts
- Füllrohrschlitten links bzw. rechts
- Füllrohrschlitten vorwärts bzw. rückwärts
- Füllrohr über Hydraulikspeicher aufwärts
- Bypassventil
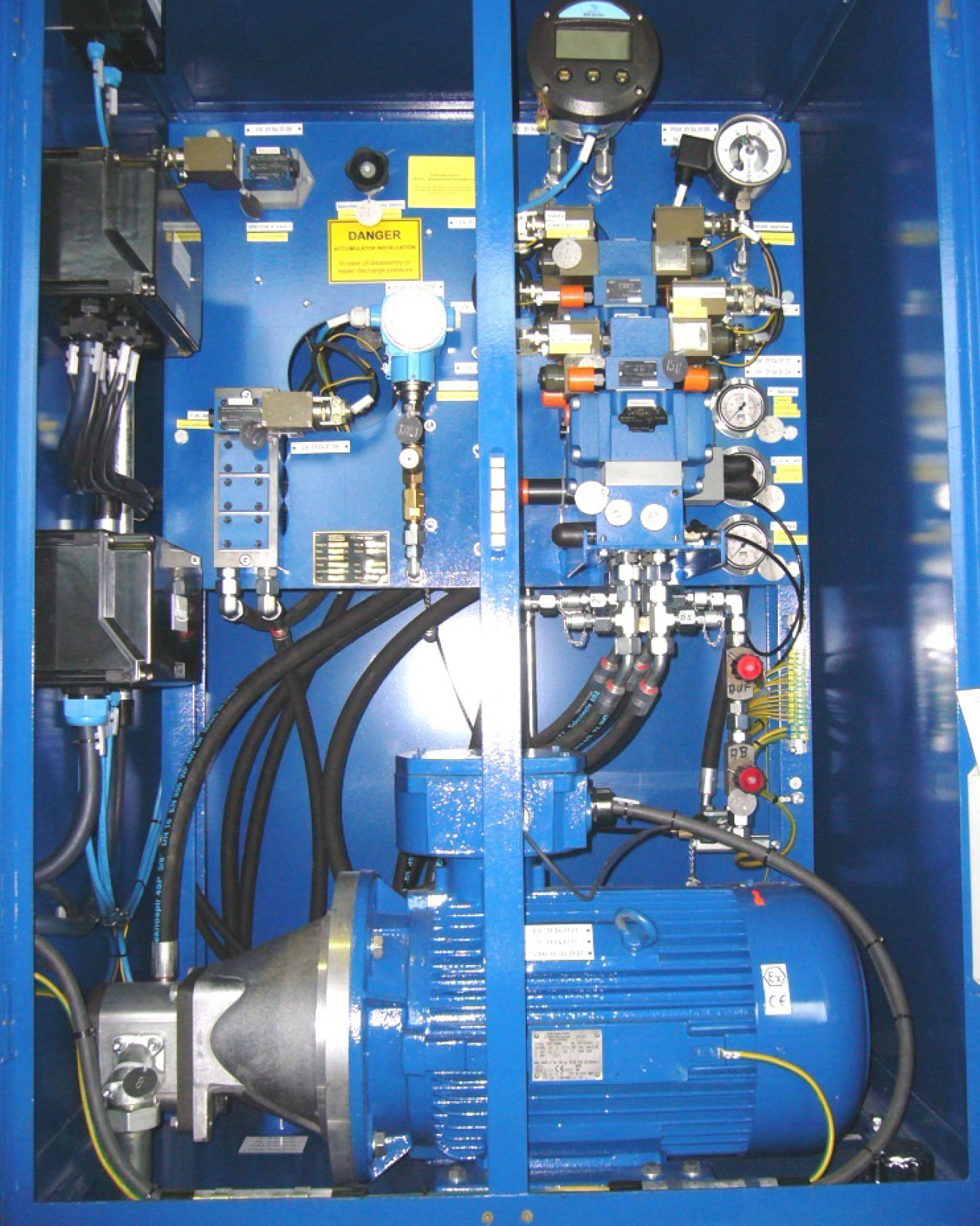
Pro Füllrohrsystem eines Gleises wird eine Pneumatikanlage installiert. Die Pneumatikanlage übernimmt die Steuerung und Überwachung des Dichtungsbalgs (Westeuropäische Kesselwagen), der Überlaufsicherung (alternativ: Sondensystem) und der Überdrucküberwachung des Kesselwagens während der Beladung. Alle Luftleitungen werden über die vertikale Schleppkette des Füllrohres auf die Luftanschlüsse des Außenrohres geführt.
Der Pneumatikschrank ist in der Regel mit einer Isolierung und einer elektrischen Heizung ausgestattet und wird am Füllrohrwagen mitfahrend montiert. Die notwendigen Verbindungskabel und -schläuche (elektrisch und pneumatisch) werden über eine Schleppkette geführt.
Allgemeines, Aktivierung Füllrohr
Die Instrumentenluft wird durch den Filter gereinigt und das Kondensat wird durch eine automatische Entleerung abgeschieden. Entsprechend des gewählten Füllrohres wird das zugeordnete 3/2-Wegemagnetventil für die Aktivierung der Überlaufsicherung, Überdrucküberwachung und Abdichtkissen auf das angewählte Füllrohr angesteuert.
Dem 3/2-Wegemagnetventil für die Befüllung des Abdichtkissens ist ein Filterregler vorgeschaltet. Vor dem 2/2-Wegeventil der Überfüllsicherung ist ein Präzisions-Druckregler eingebaut.
Überlaufsicherung
Mit Aktivierung eines Füllrohres werden die Druckleitungen der Überlaufsicherung und Druckausgleichsleitung auf das entsprechende Füllrohr geschaltet. Die Luftleitungen der Überlaufsicherung und der Druckmessung sind dadurch mit dem Überlaufsicherungsschlauch und der Druckmessleitung des aktivierten Füllrohres verbunden.
Bei der Inbetriebnahme des Füllrohrsystems wird die Überlaufsicherung so eingestellt, dass die Abschaltung der Überlaufsicherung bei der maximal zugelassenen Füllhöhe erfolgt.
Alternativ zur pneumatischen Überfüllsicherung bieten wir auch spezielle Sonden zur Grenzwertabschaltung an. Fordern Sie hierzu separate Informationen per Email an.
Druckmessung Gasphase
Mit Aktivierung eines Füllrohres wird die Druckausgleichsleitung auf das entsprechende Füllrohr geschaltet. Die Luftleitung des Drucktransmitters ist dadurch mit der Druckmessleitung des aktivierten Füllrohres verbunden.
Dadurch kann der Druck in dem Kesselwagen überwacht werden. Im Fall einer Druckerhöhung in der Gasleitung auf bis zu 300 mbar (länderspezifisch) wird der Füllvorgang automatisch abgeschaltet.
Vorteile der SCHERZER Füllrohrtechnik
Unsere robusten Füllrohre werden in hochwertiger Maschinentechnik hergestellt, mit einem Gewicht von ca. 1.600-1.850 kg. Zahlreiche unserer gelieferten Füllrohre sind seit über 30 Jahren erfolgreich im Einsatz. Die Rohre haben Wandstärken von 10-20 mm, geschliffene und hartverchromte Führungsflächen sowie Teile aus Messing oder Rotguss, inklusive einer NBR-Dichtplatte (Osteuropäische Kesselwagen). Für osteuropäische Kesselwagen ist die Dichtplatte federnd gelagert und mit stabilen Messingleisten geschützt. Die Überfüllsicherung, Überdrucksicherung und kontinuierliche Beladezustandsanzeige gewährleisten hohe Betriebssicherheit.
Die Gasrückführung erfolgt durch ein separates, hochwertiges Teleskoprohr mit Mehrfachabdichtung, um Kondensatbildung zu vermeiden. Ein flexibler Kompensator erlaubt das Auslenken des Schutzrohres und des Innenrohres, ohne dass das Füllrohr zentriert werden muss (außer für osteuropäische Kesselwagen). Während des gesamten Beladevorgangs liegen die Pratzen fest auf dem Dom, wodurch keine Scheuerbewegungen am Dichtungsbalg auftreten und die Lebensdauer der Bälge hoch ist.
Die hydraulisch ferngesteuerte Längs- und Querverfahrung ermöglicht eine präzise Positionierung. Die Abdichtung nach dem Ausfahren aus dem Kesselwagen erfolgt durch zwei O-Ringe, wodurch Restmengen von den Rohrwänden abtropfen und bei der nächsten Beladung in den Kesselwagen entleert werden (max. ca. 10-15 Liter).
In den letzten 40 Jahren haben wir mehr als 350 Füllrohre in verschiedenen Ländern montiert und in Betrieb genommen. Unsere stetige Weiterentwicklung resultiert in einem Füllsystem, das den aktuellen Stand der Technik repräsentiert und sich unter extremen Bedingungen in jahrzehntelangem Dauerbetrieb bewährt hat.
Der SPS-gesteuerte Beladevorgang erfüllt alle Sicherheitsanforderungen. Auf Wunsch kann jede Füllrohrposition visuell dargestellt und der Füllrohrhub abhängig vom Kesselwagentyp begrenzt werden.
Eine übersichtliche Zusammenfassung finden Sie in unseren Broschüren unter Downloads.
Erfahren Sie hier mehr über unsere Einzelbereiche der Kesselwagen Umschlagsysteme
On-Spot-Anlagen Einzel- und Reihenbeladung Untenbeladung Entladeanlagen